Modern consumers not only pay attention to material performance, but also pay more attention to appearance texture and surface characteristics. Through different surface treatment technologies, stainless steel plates can achieve a variety of visual and tactile effects such as mirror, matte, brushed, titanium, etching, embossing, etc., to enhance their artistic beauty and practical value.
This article will comprehensively introduce the common surface treatment types, processing technology, technical characteristics and applicable scenarios of stainless steel plates to help you understand and choose the most suitable surface treatment method.
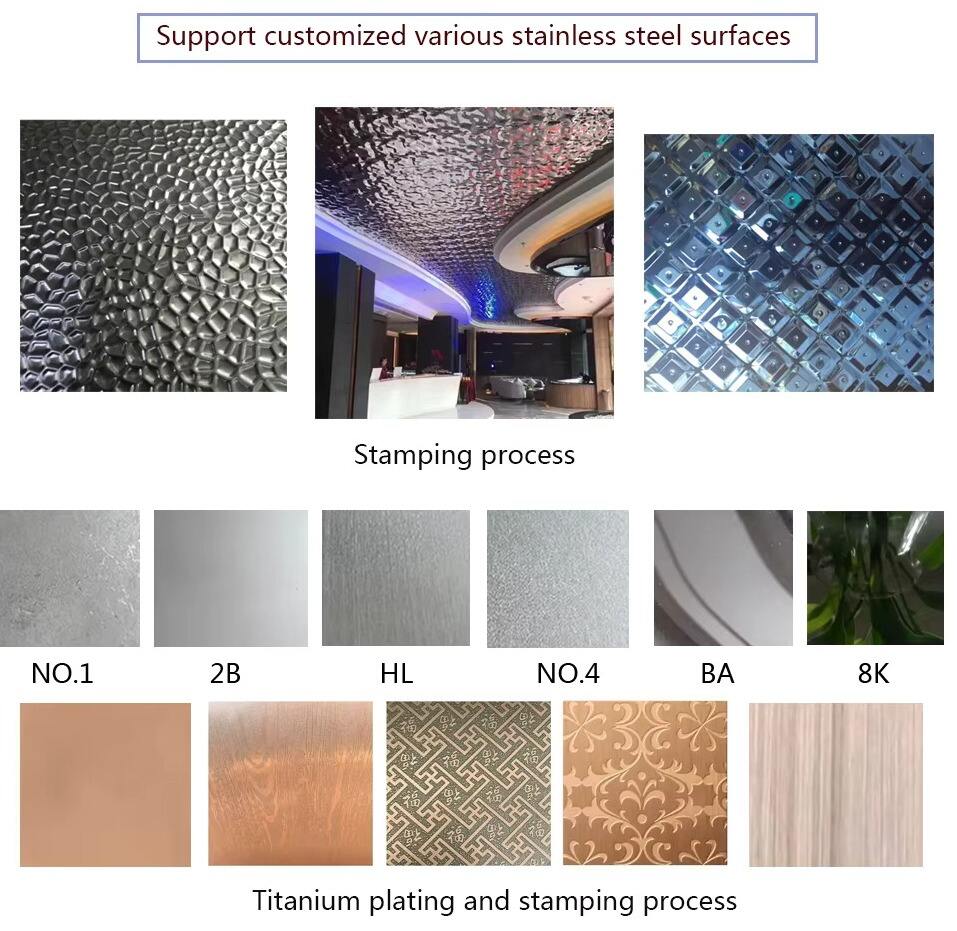
Why Do Stainless Steel Plates Need Surface Treatment?
In the metal processing industry, surface treatment is not only a means of beautification, but also a key step to improve the performance of stainless steel:
Improve decorativeness: Through processing, visual effects such as mirror, matte, brushed, etc. can be achieved to enhance the overall aesthetics.
Enhance corrosion resistance: Certain treatments such as electroplating and passivation can enhance the oxidation resistance of the stainless steel surface.
Increase hardness and wear resistance: For example, titanium and PVD coatings can improve surface strength.
Improve processing performance: Certain surface treatments help with subsequent bending, welding, stamping and other operations.
Meet functional requirements: Anti-fingerprint and antibacterial treatments are used in specific application areas (such as medical and electronics).
Common Processes For Stainless Steel Surface Treatment
1. Mirror Panel (8K Mirror)
Mirror panel usually refers to a surface treatment method that uses mechanical or electrochemical polishing to make the stainless steel surface as smooth and reflective as a mirror. It is often called "8K mirror" in the industry.
Processing method:
Mainly mechanical polishing, with polishing pastes and cloth wheels of different particle sizes, gradually fine grinding, and finally forming a mirror gloss; electrolytic polishing can also be used to obtain a smoother and more uniform mirror effect.
Advantages:
- High reflectivity, beautiful and elegant
- Dense surface, easy to clean
- Widely used in elevators, decorations, kitchenware, mirrors, accessories, etc.
Disadvantages:
- Easy to stick fingerprints and oil stains
- Average scratch resistance
- High requirements for processing environment
2. Wire Drawing Plate
Wire drawing is to form fine filamentary textures on the surface of stainless steel through mechanical friction. Common effects include straight lines, random lines, ripples, snowflakes, etc., with a soft metallic texture.
Processing method:
Use a special wire drawing machine or belt sander to adjust the depth and thickness of the texture according to the coarseness of the sandpaper.
Advantages:
- High-end, widely used in architectural decoration, electrical panels, doors and windows, kitchen and bathroom products
- Can cover minor scratches
- Soft visual, anti-glare
Disadvantages:
- Easy to leave fingerprints and stains
- Texture directionality is strong, need to pay attention when designing
3. Titanium Plate (PVD Vacuum Coating)
Titanium plate refers to a layer of titanium or other alloy layer deposited on the surface of stainless steel plate through PVD (physical vapor deposition) technology to form noble colors such as gold, rose gold, black titanium, champagne gold, etc., which are often used in high-end architecture and decoration fields.
Processing method:
Titanium or other metals are evaporated under vacuum conditions and deposited on the surface of stainless steel to form a nano-scale film, which is firmly bonded.
Advantages:
- Rich color and good stability
- Strong corrosion resistance and scratch resistance
- Luxurious and elegant decorative effect
Disadvantages:
- High cost
- Not suitable for strong impact scenes
4. Etching Plate Process
Etching is a common process for pattern decoration on stainless steel surface. It is usually used in combination with mirror or titanium plate. The pattern is etched out by chemical corrosion to form a concave and convex, light and shadow effect.
Processing method:
Coating corrosion-resistant layer → pattern exposure → corrosion → cleaning → surface treatment (such as passivation, coloring, PVD, etc.)
Application range:
Mostly used in elevator decorative panels, hotel background walls, doorplates, wall decoration and other scenes.
5. Sandblasting Plate Process
Sandblasting is to spray quartz sand, glass beads, etc. onto the surface of stainless steel through high-pressure airflow, thereby forming a uniform matte texture with good matte and shielding effects.
Features:
- Soft and non-reflective surface
- Strong anti-fingerprint ability
- Applied to industrial equipment and decorative components
6. Embossed Plate Process
Embossed is a process of mechanical rolling or molding on the surface of stainless steel plate to form a relief pattern. Common patterns include water ripples, squares, leather grain, diamonds, etc.
Advantages:
- Good anti-slip performance
- Beautiful and practical
- Can cover scratches and flaws
Application scenarios:
Elevators, floor pedals, wall decorations, door panels, etc.
7. Colored Stainless Steel Process (Coloring/Electroplating)
In addition to titanium, there are many color processing processes on the market, such as chemical coloring, electrochemical coloring, etc., which can give stainless steel a variety of color changes, such as blue, coffee, bronze, etc.
8.No.1, 2B, BA And Other Basic Surface Treatments
- Rough surface after annealing and pickling after hot rolling
- Suitable for industrial use, such as boilers, pressure vessels, etc.
- Annealing and pickling after cold rolling, and then light cold rolling to form a matte surface
- Commonly used in kitchenware, construction, and medical equipment
- BA surface (Bright Annealed):
- Cold-rolled plate brightly annealed in a protective atmosphere
- Bright surface, suitable for deep drawing
Anti-Fingerprint Stainless Steel Treatment
In order to solve the problem of easy fingerprints on mirror and titanium surfaces, anti-fingerprint coating (AF coating) is often used to effectively prevent grease adhesion and improve the user experience.
The richness and complexity of stainless steel surface treatment technology give stainless steel plates more design freedom and practical value. From traditional mirrors and brushed to advanced titanium, etching, embossing, and the emerging functional surface treatment, the appearance and performance of stainless steel are no longer a single form.
For users, correctly selecting the type of surface treatment can not only improve the product quality, but also extend the service life and optimize the cost structure. I hope that the systematic introduction in this article can help you make more scientific and accurate decisions in material selection or product design.
HNJBL is a professional steel manufacturer and supplier. Our company's main products include carbon steel, stainless steel, wear-resistant steel, steel profiles, coated steel, etc. Complete specifications, stable quality, and sufficient quantity.
+86 17611015797 (WhatsApp )
info@steelgroups.com