As a special equipment that withstands internal or external pressure, pressure vessels are widely used in chemical, petroleum, medicine, energy, food, aerospace and other fields. Since they often face extreme working conditions such as high temperature, high pressure and corrosion during operation, they place extremely high demands on the selection of materials. The selection of materials is not only related to the safety and reliability of pressure vessels, but also directly affects the manufacturing cost and service life. This article will discuss in detail the ideal materials for manufacturing pressure vessels.
Basic Requirements For Pressure Vessel Materials
As a long-term pressure-bearing equipment, the material of the pressure vessel must first have excellent mechanical properties. This includes high tensile strength, good ductility, impact toughness and fatigue strength. The material must not crack under high pressure and be able to absorb energy instead of breaking when impacted by external force. In addition, thermal stability and high temperature resistance are also important indicators for judging materials, especially in high-temperature reactors and heat exchange equipment, where the material must maintain stable structure and mechanical properties.
Corrosion resistance is another key requirement. Many pressure vessels are used to store or react corrosive media such as strong acids, strong alkalis, salt solutions, organic solvents, etc. The corrosion resistance of the material directly determines the service life and safety factor of the equipment. The material must also have good welding performance and processing and forming capabilities to meet the manufacturing needs of complex structures.
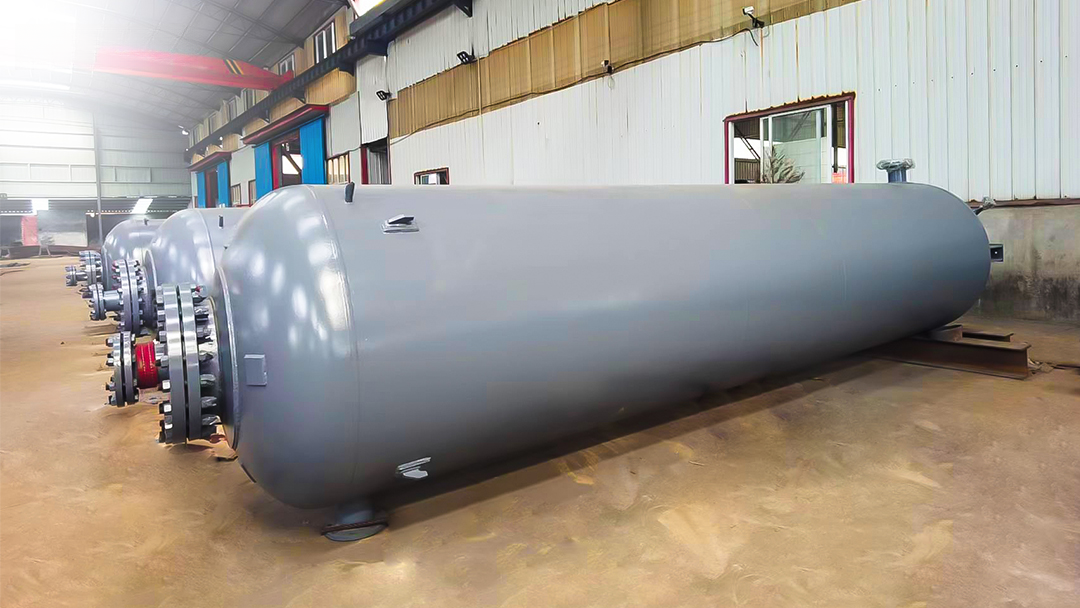
What Materials Can Be Used To Manufacture Pressure Vessels?
Carbon Steel:
Carbon steel is the most commonly used material in pressure vessels. It is selected for its good mechanical properties, strong weldability, good processing performance and low price. Common carbon steel materials include Q235, Q345, A516Gr.70, etc.
The yield strength of carbon steel material is moderate, which is suitable for making most pressure-bearing parts, especially in an environment with normal temperature and no strong corrosive media. Its good ductility makes it easy to form and weld in manufacturing, which greatly simplifies the manufacturing process. In addition, carbon steel materials have perfect standards and supply systems at home and abroad, which is convenient for quality control.
However, the disadvantages of carbon steel are also obvious. Its corrosion resistance is poor, and it is easy to rust in acidic, alkaline or salt environments. If reasonable anti-corrosion measures are not taken, perforation and leakage are very likely to occur. In addition, its toughness drops sharply in low-temperature environments, and there is a risk of brittle fracture, which limits its application in low-temperature occasions.
Therefore, carbon steel is mainly used in the following occasions:
- Air compression storage tanks;
- Water treatment systems;
- Boilers;
- Oil storage tanks, etc.
In order to improve the corrosion resistance of carbon steel, it is often protected by lining, spraying, etc. Although carbon steel has disadvantages, its excellent comprehensive cost performance makes it still an indispensable basic material in the manufacture of pressure vessels.
Alloy Steel:
Alloy steel is a type of material that improves performance by adding alloy elements such as chromium, nickel, and molybdenum to carbon steel. Its biggest advantage is high mechanical strength, good thermal strength, and certain corrosion resistance. Commonly used alloy steels include 15CrMoR, 12Cr1MoV, SA387Gr.11, Gr.22, etc., which are widely used in high-temperature and high-pressure containers, such as steam boilers, reactors, etc.
After adding chromium and molybdenum, the oxidation resistance and creep strength of alloy steel are significantly improved, so that it can maintain good stability even in high temperature and high pressure environments. Some alloy steels can also provide corrosion resistance to specific media, such as 12Cr1MoV, which performs well in high temperature hydrogen sulfide environments.
Although alloy steel has excellent performance, its manufacturing cost is significantly higher than that of ordinary carbon steel, and its processing difficulty is also greater. During welding, process parameters need to be strictly controlled, and heat treatment should be performed to avoid thermal cracking and stress corrosion cracking. In addition, some alloy steels are sensitive to hydrogen embrittlement and need to be used with caution in hydrogen storage equipment.
Stainless Steel:
Stainless steel can also be used to manufacture pressure vessels, especially in the fields of chemical, pharmaceutical and food, and its excellent corrosion resistance makes it the first choice. Stainless steel is mainly divided into austenitic, ferritic, martensitic and duplex stainless steel. The most commonly used austenitic stainless steels such as 304, 316L, etc. are widely used due to their good weldability, toughness and corrosion resistance.
316L stainless steel has good resistance to chloride media due to its high molybdenum content, and is particularly suitable for pressure vessels in saline or seawater environments. Duplex stainless steel (such as 2205, 2507) combines the advantages of austenite and ferrite structures, has higher strength and pitting resistance, and has gradually replaced its position in some traditional austenitic stainless steel fields.
The main disadvantage of stainless steel is its high price, especially for models with high nickel and molybdenum content. In addition, intergranular corrosion is easily formed during welding, and solid solution treatment or low-carbon models (such as 316L) are required. In a strong reducing environment, stainless steel may have the risk of stress corrosion, and the material model needs to be selected in a targeted manner.
Therefore, stainless steel is mainly used in the following occasions:
- Reactor;
- Pharmaceutical storage tank;
- High-purity gas storage tank, etc.
Titanium and Titanium Alloys:
Titanium metal has become a popular material for the manufacture of high-end pressure vessels due to its low density, high specific strength and excellent corrosion resistance. Titanium has excellent stability to a variety of highly corrosive media such as nitric acid, organic acids, wet chlorine gas, seawater, etc., and is particularly suitable for long-term use in oxidizing and neutral environments.
Common titanium materials include pure titanium (such as TA1, TA2) and titanium alloys (such as TC4). Pure titanium has excellent weldability and formability, and is widely used in containers with low strength but high corrosion resistance requirements, such as brine storage tanks, electroplating tanks, chemical reactors, etc. Titanium alloys have both strength and corrosion resistance, and are suitable for pressure-bearing parts or high-stress occasions.
Titanium materials are expensive, difficult to process, and have extremely high environmental requirements during welding (inert gas protection is required), so they are mostly used in high-tech and high-value-added products. In the fields of aerospace, aviation, deep-sea engineering, seawater desalination equipment, medical equipment, etc., titanium materials are increasingly playing an irreplaceable role.
How To Choose?
In actual engineering, the material selection varies under different working conditions. Taking the refinery desulfurization tower as an example, its medium contains highly corrosive components such as hydrogen sulfide, ammonia, and chlorides. It is more appropriate to choose 316L stainless steel or 2205 duplex stainless steel. In power plant boilers, high temperature and high pressure steam places extremely high demands on high temperature resistant alloys, and 12Cr1MoV or SA387 alloy steel is often used.
In the fertilizer industry, high pressure reactors used in synthetic ammonia units often use special materials such as titanium composite plates and Hastelloy composite plates; in the food processing industry, in order to ensure hygiene and cleanliness, austenitic stainless steel materials such as 304L and 316L are often used.
Therefore, in engineering applications, material selection must be combined with equipment working pressure, temperature, medium type, operation cycle, economy, and standard applicability. Consider a variety of factors to select materials that are both safe, reliable, and economically reasonable.
HNJBL is a professional steel manufacturer and supplier. Our company's main products include carbon steel, stainless steel, wear-resistant steel, steel profiles, coated steel, etc. Complete specifications, stable quality, and sufficient quantity.
+86 17611015797 (WhatsApp )
info@steelgroups.com