Țevi sudate din oțel inoxidabil sunt utilizate în mod larg în diverse industrii și domenii de construcții datorită excelentei lor rezistențe la coroziune și forță. Tehnologia de sudare este un pas cheie în fabricație Țevi sudate din oțel inoxidabil . Alegerea tehnologiei adecvate de sudare nu numai că poate îmbunătăți calitatea tuburilor sudate, dar și să optimizze eficiența producției.
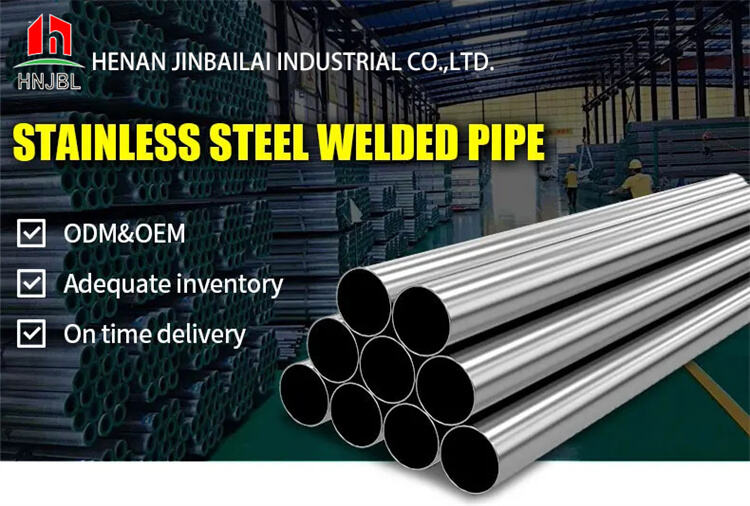
Ce este o țeavă sudată din oțel inoxidabil?
Tuburile din oțel inoxidabil sudate, denumite simplu tuburi sudate, sunt tuburi fabricate prin sudarea oțelului sau a bandei de oțel după cum acestea au fost rulate și formate cu ajutorul unităților și matricelor. Tuburile din oțel sudate au proceese de producție simple, o productivitate ridicată, multe tipuri și specificații, dar rezistența lor generală este mai mică decât cea a tuburilor din oțel fără joncțiuni.
Ce Tehnologii de Solderare Există pentru Tuburi Solderate din Oțel Inoxidabil?
Procesul de producție al tuburilor din oțel inoxidabil sudate include, în mod obișnuit, etapele de formare, sudare, răcire, dreptecare, tratament superficial și alte legături. Sudarea este cea mai critică etapă, care determină calitatea și performanța tuburilor sudate. Tehnici comune de sudare includ sudarea TIG, sudarea cu gaz, sudarea sub arc cu scori, sudarea manuală cu arc și sudarea MIG/MAG.
1. Sudarea TIG (sudarea cu arc argonic):
Sudarea TIG (Tungsten Inert Gas Welding) este abrevierea pentru sudarea cu protecție a arcului electric prin gaze inernte (de obicei argon). Este o tehnologie care folosește un arc electric și un gaz inert (de obicei argon) pentru a proteja zona sudată. Această tehnologie utilizează un electrod din tungsten ca electrod de sudare, iar argonul este folosit pentru a proteja arc-ul și zonă de sudare împotriva oxigenării și contaminării.
Avantaje ale sudării TIG: calitate ridicată a zonei sudate, deformare mică, puține pori, puține crăpături, bună performanță la sudare și lipsă de proiecții în timpul procesului de sudare.
Inconvenient ale sudării TIG: viteză de sudare lentă, cost ridicat, operație dificilă, cerințe ridicate privind stabilitatea sursei de alimentare și nu este potrivită pentru sudarea la curent ridicat.
Aplicație: Sudarea cu arc în argon este potrivită pentru aplicații industriale cu cerințe ridicate, cum ar fi aerospațial, echipamente chimice și decorarea arhitecturală de lux. Datorită procesului său stabil de sudare și calității ridicate, este foarte potrivită pentru fabricarea tuburilor din oț inoxidabil sudate cu precizie.
2. Sudarea cu gaz:
Sudura cu gaz este o tehnologie de sudură care folosește combustia gazelor pentru a genera o flacăru de înaltă temperatură care să liquefie tuburile din oțel inoxidabil sudate. Gazele combustibile folosite sunt, printre altele, etilenul și oxigenul. Temperatura flacării se ajustează prin controlul raportului de gaze pentru a realiza sudarea materialelor. Gazele combustibile utilizate în sudura cu gaz includ etilen, metan, gaz propan-butanol lichid, etc. Etilenul este cel mai folosit în prezent în producție. Deoarece etilenul eliberează cea mai mare cantitate de căldură și are cea mai ridicată temperatură a flacării la arzirea în oxigen pur, care poate ajunge la 3150 de grade Celsius, aceasta este de obicei numită flacără oxietilene.
Avantaje ale sudurii cu gaz: echipamentul de sudare are o structură simplă, este ușor de menținut și are un cost redus.
Dezavantaje ale sudurii cu gaz: calitatea sudării este instabilă, sudura cu gaz are cerințe de control ridicate privind procesul de sudare și este ușor influențată de mediul de lucru și de tehnologia de operare.
Aplicație: Sudura cu gaz este de obicei folosită pentru sudarea tuburilor din oțel inoxidabil de mică grosime, și este potrivită pentru reparații relativ simple în teren și sarcini de sudare mici, cum ar fi repararea conductelor casnice și sudarea structurilor ușoare.
3. Sudura cu arc sub flux:
Sudura cu arc sub flux (SAW) este o metodă de sudare în care arcușul este ascuns sub stratul de flux. Fluxul formează un strat protector în timpul procesului de sudare pentru a preveni oxigenarea și contaminarea. Arcușul generează căldură prin stratul de flux și topirea zonei de sudare a tubului din oțel inoxidabil.
Avantaje ale suturei cu arc sub flux: Deoarece arcușul este ascuns sub stratul de flux, viteza de sudare este rapidă, sutura este uniformă, procesul de sudare este stabil, iar rezistența suturei este mare.
Dezavantaje ale suturei cu arc sub flux: Sunt necesare echipamente speciale de sudare cu arc sub flux și flux, iar investiția în echipament este mare; procesul de sudare este relativ complicat și necesită abilități și experiență profesionistă.
Aplicație: Saldarea cu arc sub flux este folosită în mod larg în producția industrială la scară largă, cum ar fi saldarea conductelor de ulei, a echipamentelor electrice și a pieselor structurale mari. Datorită eficienței sale ridicate și calității excelente de saldare, este potrivită pentru situații cu salduri lungi și cerințe mari de producție.
4. Saldarea manuală cu arc (SMAW):
Saldarea manuală cu arc (Saldarea protejată cu metal) este o metodă de saldare prin căldura generată de arc și de electrodu. Stratul exterioar al electroduei este acoperit cu o stratificare protectivă care previne oxidarea zonei saldate. Electroda se topesc continuu în timpul procesului de saldare pentru a forma o saldare.
Avantajele saldării manuale cu arc: Echipamentul de saldare manuală are o structură simplă, este convenabil pentru operațiuni în teren și are un cost relativ scăzut; poate săldeze materiale de diferite grosimi și forme și are o adaptabilitate puternică.
Contra ale salderii cu arc manual: Calitatea saldării este influențată în mod semnificativ de abilitățile saldatorului și de condițiile ambientale, iar proiecții și fumul generat în timpul saldării pot afecta, de asemenea, calitatea saldării; comparativ cu metodele automate de saldare, saldarea manuală are o eficiență mai scăzută a producției.
Aplicație: Salderia cu arc manual este utilizată pe scară largă în diverse operațiuni de teren și lucrări de întreținere, mai ales pentru sarcini de saldare cu condiții complexe de teren și locații speciale, cum ar fi construcțiile și reparațiile echipamentelor pe teren.
5. Saldarea MIG/MAG:
Saldarea MIG (Metal Inert Gas) și MAG (Metal Active Gas) sunt metode de saldare care folosesc un arc și o fir continuu alimentat. Saldarea MIG utilizează un gaz inert (cum ar fi argon), în timp ce saldarea MAG utilizează un gaz activ (cum ar fi dioxidul de carbon). Ambele metode topesc și umplu solda cu un fir continuu alimentat.
Avantaje ale sudurii MIG/MAG: viteză rapidă de sudare, potrivită pentru producție la scară largă și sudarea unor legături lungi; suduri uniforme, puține defecțiuni, proces stabil de sudare; grad ridicat de automatizare, ușurință de operație și reducerea intervenției manuale.
Dezavantaje ale sudurii MIG/MAG: se necesită echipamente speciale și sistem de aprovizionare cu gaz, iar investiția în echipamente este mare; costul gazului este ridicat, ceea ce crește costurile de producție.
Aplicație: sudarea MIG/MAG este potrivită pentru producția industrială la scară largă, cum ar fi fabricarea de autoturisme, construcția navală și ingineria civilă. Datorită vitezei sale eficiente de sudare și calității excelente de sudare, este folosită pe scară largă în diferite nevoi industriale de sudare.
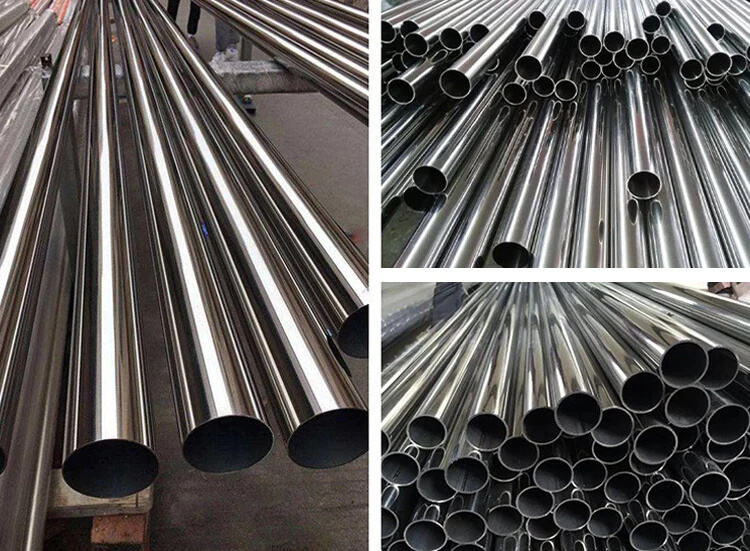
Există multe tipuri de tehnologii de sudurare pentru tuburi din oțel inoxidabil sudate, și fiecare tehnologie are avantaje și limite unice. Înțelegerea caracteristicilor diferitelor tehnologii de sudare și selectarea metodelor adecvate în funcție de nevoile reale de producție poate îmbunătăți eficient calitatea și eficiența de producție a tuburilor sudate.
Află mai multe despre produs:
Email:info@steelgroups.com
WhatsApp: +86 17611015797