Chapa de aço galvanizado é um material composto de aço e zinco. Produtos galvanizados combinam as vantagens desses dois materiais. O material composto tem a força e plasticidade do aço e uma camada protetora resistente à corrosão. É amplamente utilizado em campos industriais como construção, eletrodomésticos e automóveis.
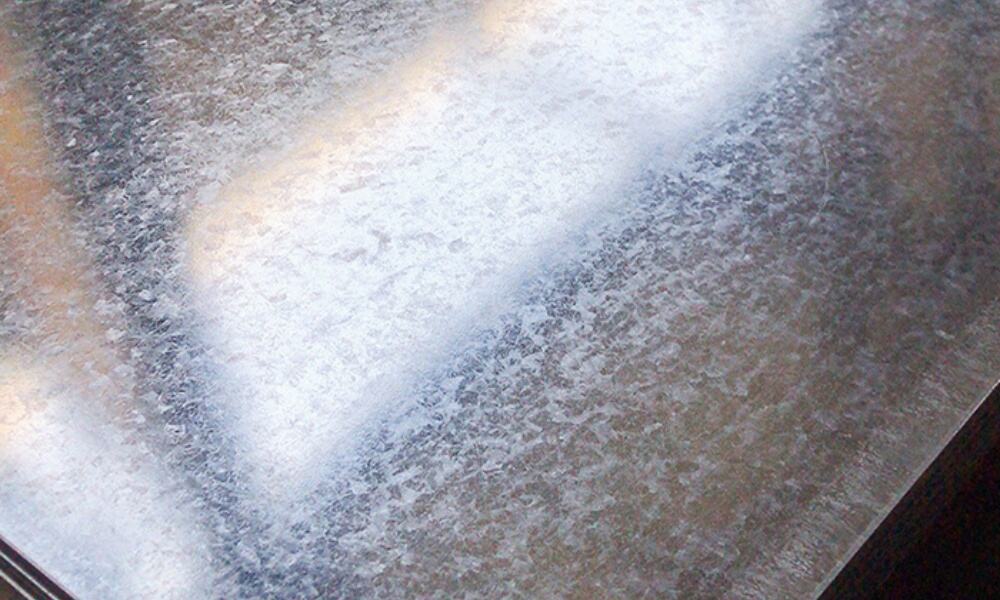
O Que é Folha de Aço Galvanizado?
Chapa galvanizada é uma folha de aço com uma camada de zinco metálico revestida na superfície do aço para proteger o substrato de aço. Como a atividade eletroquímica do zinco é maior do que a do ferro, a presença da camada de zinco pode retardar a oxidação e corrosão do aço. A espessura comum chapas de Aço Galvanizado geralmente está entre 0,25mm e 5mm, e há muitas especificações para escolher de acordo com diferentes requisitos de aplicação.
Mecanismo de Resistência à Corrosão da Folha de Aço Galvanizado:
A resistência à corrosão chapa de aço galvanizado vem do efeito protetor da camada de zinco. Seu princípio de funcionamento é alcançado principalmente através de três mecanismos, a saber: efeito de barreira física, efeito de anodo de sacrifício e fenômeno de passivação durante a corrosão.
Efeito de barreira física
Como a camada mais externa de chapa galvanizada , a camada de zinco isola o contato direto entre ar e umidade e o aço por meio do efeito de barreira física, impedindo assim a oxidação e a ferrugem. O próprio zinco possui boa resistência à oxidação. A espessura do revestimento determina a duração do efeito protetor. Quanto mais grossa for a camada de zinco, mais significativo será o efeito físico de proteção fornecido.
Efeito de anodo de sacrifício
Quando o placas de aço galvanizadas é parcialmente exposto à superfície do aço devido ao desgaste mecânico ou corrosão química, o "efeito de anodo de sacrifício" do zinco começa a entrar em ação. O zinco tem um potencial mais baixo que o aço e uma atividade eletroquímica maior. Ele irá oxidar preferencialmente para proteger o aço da corrosão. Essa característica permite que o placas de aço galvanizadas para prolongar sua vida útil, mesmo quando o revestimento está danificado, mostrando alta resistência à corrosão.
Fenômeno de passivação durante a corrosão
Em um ambiente úmido ou com presença de oxigênio, um fino filme de óxido ou carbonato de zinco básico se formará na superfície da camada de zinco. Este filme de passivação pode reduzir ainda mais a taxa de corrosão, tornando o painel de aço galvanizado com boa resistência à corrosão em várias condições ambientais severas.
Tipos de Processo de Galvanização:
Atualmente, os processos de produção de chapas de Aço Galvanizado incluem principalmente galvanização a fogo e galvanização eletrolítica:
Galvanização a fogo: O aço é imerso em uma solução de zinco fundido para formar um revestimento de zinco por adesão física e reação química. Neste processo, a camada de zinco é mais grossa (geralmente mais de 50 micrômetros), oferece um efeito protetor mais forte e possui alta resistência à corrosão. É adequado para materiais de construção expostos à atmosfera e componentes de aço em ambientes severos.
Eletro-galvanização: O zinco é fixado uniformemente à superfície do aço utilizando o princípio de deposição eletrolítica. O revestimento é mais fino (geralmente menos de 20 micrômetros) e possui uma superfície mais suave. Normalmente é usado para produtos que exigem alta precisão ou requisitos estéticos elevados. Embora sua resistência à corrosão não seja tão boa quanto a de a quente chapas de Aço Galvanizado , ele tem um bom desempenho em ambientes internos ou com baixa corrosividade.
O Papel Do Revestimento Galvanizado:
A camada de zinco fornece uma barreira física eficaz para a chapa de aço, impedindo que a umidade e o oxigênio externos entrem em contato direto com o aço, reduzindo assim a taxa de corrosão da chapa de aço. Ao mesmo tempo, como material de anodo sacrificial, o mecanismo de proteção eletroquímica do zinco pode melhorar ainda mais o efeito anti-corrosivo.
Fatores Que Afetam A Resistência À Corrosão Das Chapas De Aço Galvanizadas:
Espessura do Revestimento de Zinco
Quanto mais espessa for a camada de zinco, maior será a resistência à corrosão. A galvanização a quente geralmente consegue uma camada mais grossa, enquanto a camada de zinco eletrodepositada é relativamente fina, e a espessura da camada pode precisar ser aumentada quando usada em um ambiente úmido.
Qualidade do processo de galvanização
A qualidade diferente do processo de galvanização também afeta diretamente a resistência à corrosão. A galvanização a quente geralmente tem melhor resistência à corrosão do que a eletrogalvanização devido à maior espessura da camada de zinco.
Qualidade do aço em si
A limpeza, planicidade, teor de carbono, etc., da superfície do aço afetam a adesão da camada de zinco. Revestimentos de aço de alta pureza e baixo teor de carbono têm melhor adesão e ajudam a melhorar a resistência à corrosão.
Condições Ambientais
As chapas de aço galvanizadas se corroem mais rapidamente quando expostas em áreas costeiras, áreas quentes e úmidas ou ambientes ácidos, então são necessárias camadas mais grossas ou manutenção regular para prolongar a vida útil.
Desempenho de Folhas de Aço Galvanizado em Diferentes Ambientes Corrosivos:
A durabilidade do placas galvanizadas em diferentes ambientes corrosivos varia. O seguinte é seu desempenho específico em vários ambientes corrosivos típicos.
Áreas Costeiras
O ar nas áreas costeiras contém alto teor de sal, o que é altamente corrosivo para materiais metálicos. A galvanização a quente chapas de Aço Galvanizado pode resistir eficazmente à corrosão por sal neste ambiente e ter uma longa vida útil, geralmente superior a 15 a 20 anos.
Áreas com poluição industrial
O ar em áreas industriais contém grande quantidade de substâncias ácidas ou alcalinas, como dióxido de enxofre e cloro, que podem causar reações químicas na camada galvanizada e acelerar o processo de corrosão. As chapas de aço galvanizado a quente podem resistir melhor aos gases ácidos, mas exigem limpeza e manutenção regulares.
Ambiente de alta umidade e alta temperatura
Ambientes úmidos e de alta temperatura podem facilmente causar a oxidação da camada de zinco em chapas de aço galvanizado, especialmente em ambientes com pouca circulação de ar. Portanto, ao usar chapas de aço galvanizado em condições de alta umidade ou temperatura, deve-se escolher uma camada de zinco mais grossa e garantir uma boa ventilação para retardar a corrosão.
Métodos de Teste de Corrosão Para Chapas de Aço Galvanizado:
Para avaliar a resistência à corrosão das chapas de aço galvanizado, os seguintes métodos de teste padrão são geralmente usados:
Teste de névoa salina
O teste de névoa salina avalia a resistência à corrosão das chapas de aço em ambientes costeiros ou de alta concentração de sal, expondo-as a ambientes de névoa salina. Após um certo período de tempo, observa-se o grau de corrosão na superfície da camada de zinco. Os resultados do teste podem refletir a força de resistência à corrosão de revestimentos de diferentes espessuras.
Teste de calor úmido
O teste de calor úmido simula a resistência à corrosão de chapas de aço galvanizado sob condições climáticas extremas (especialmente climas tropicais e marítimos) colocando-as em um ambiente de alta temperatura e alta umidade. Este experimento é adequado para testar a durabilidade geral e estabilidade dos revestimentos das chapas de aço.
Teste de exposição ao ar livre
Ao expor chapas de aço galvanizado no ambiente natural, seu desempenho é monitorado por um longo período. Este teste pode obter dados mais realistas sobre durabilidade, mas o ciclo é longo e normalmente leva vários anos para obter dados de teste completos.
Áreas de Aplicação das Chapas de Aço Galvanizado:
Indústria da Construção: chapas de Aço Galvanizado podem ser usadas para componentes de construção, como telhados, painéis de parede e tubos.
Fabricação de automóveis: chapas de aço galvanizado podem ser usadas para carrocerias e chassis.
Eletrodomésticos: chapas de Aço Galvanizado são usadas principalmente para as carcaças externas de geladeiras, máquinas de lavar, entre outros.
Indústria de energia e potência: folhas de aço galvanizadas são usadas para as carcaças externas de equipamentos de energia e estruturas, como torres de transmissão.
Instalações de transporte: chapas de Aço Galvanizado são usadas na fabricação de instalações públicas, como pontes, guardrails e sinais de trânsito.
Com o avanço da tecnologia, a adição de materiais compósitos resistentes à corrosão às folhas de aço galvanizado e a pesquisa e desenvolvimento de revestimentos autoreparáveis aumentarão ainda mais seu valor de aplicação no futuro. Em aplicações práticas, escolher o processo de galvanização e a espessura adequados de acordo com as características ambientais e os requisitos do projeto é fundamental para garantir o uso a longo prazo e estável de folhas de aço galvanizado em vários ambientes.
Somos um fabricante profissional de diversos produtos de aço com especificações completas. Entre em contato conosco!
+86 17611015797 (WhatsApp )
info@steelgroups.com