Pocinčana cijev je uobičajeni materijal za gradnju i industriju. Njena površina je obložena slojem cinka kako bi se željezni elementi unutar čelikaste cijeve spriječili od dodira s vanjskim zrakom i vlagošću, time igrajući ulogu protiv korozije i oksidacije. Međutim, mnogi korisnici su primijetili da se galvanizirane čelikaše cijevi mogu oksidirati tijekom korištenja galvaniziranih cijevi. Dakle, zašto se galvanizirana cijev oksidira? Koja je uzrokovanja oksidaciji galvaniziranih cijevi? I kakav će utjecaj njihova oksidiranja imati na stvarno korištenje? Ovaj članak će detaljno objasniti ove probleme, i nadam se da će vam biti koristan.
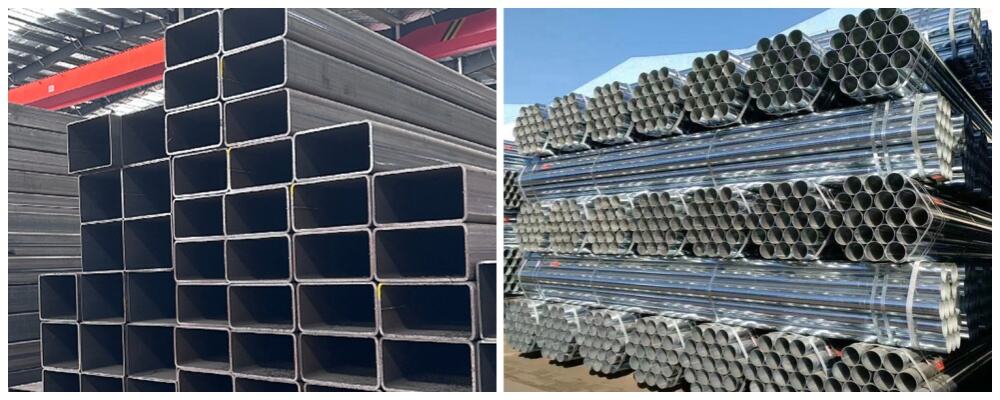
Što je galvanizirana cijev?
Cinkovana cijev je cijev koja formira protupropadnu sloju tako što na površinu očeljane cijevi namješta sloj cinka kako bi se poboljšao otpor propada cijevi. Cilj cinkovanja je sprečavanje samog propada cijevi od oksidativnog korozije zbog dodira s medijima poput zraka i vode. Posebno u upotrebi u tužnim okruženjima kao što su vlaga i sol, cinkovani sloj pruža izvrsnu zaštitu.
Prema različitim postupcima cinkovanja, cinkovane cijevi se mogu podijeliti na cinkovane toplom i cinkovane elektrodepozicijom.
- Cinkovana cijev toplom: Postupak cinkovanja toplom je zagrijati očeljenu cijev do određene temperature i potonuti je u posudi s tekućim cinkom. Putem kemijskih reakcija, cinkovi sloj se spoji s površinom očeljane cijevi da bi se formirao sloj cinkovo-željezne legure. Sloj cinka na cinkovanoj cijevi toplom je deblji, obično do 60-80 mikrona, i ima odličan otpor propada.
- Elektrogalvanizirana cijev: Zinčana sloja se nalazi na površini oceljske cijevi putem elektrodepozicije ili spremanja. Zinčana sloja elektrogalvanizirane cijevi je relativno tanka, obično između 5-15 mikrona. Iako je protupodmorski učinak lošiji od toplorazvitog galvaniziranja, jednolikost zinčane sloje može se kontrolirati tijekom obrade.
Protupodmorski princip galvaniziranja
Protupodmorski princip galvanizirane cijevi zavisi od "žrtvenog anoda" efekta zinca. Metalna aktivnost zinčane sloje je jaka. Kada se površina cijevi dotakne vanjskom okruženju, zinac će prvo prodjeliti oksidacijsku reakciju i formirati zinčastu ržu (ZnO). Ova sloja zinčaste rže može izolirati daljnji utjecaj kiseonika i vlažnosti te zaštititi tijelo oceljske cijevi od korozije.
Zašto se galvanizirana cijev s Kori?
Iako teoretski sloj cinka na cijevima s galvanizacijom može učinkovito sprečavati koroziju, u praksi se ržajošća može još uvijek pojaviti. Razine ržađenja galvaniziranih cijevi su obično sljedeće:
Oštećenje cinskega sloja:
Zaštitni sloj na površini galvanizirane cijevi sastoji se od cinskega sloja. Ako je taj sloj pod utjecajem mehaničkog udara, nošenja, šupljina i drugih faktora tijekom upotrebe, cinski sloj može otopiti ili se slomiti, a otvorena površina čelika će biti izložena vanjskom okruženju i podložna koroziji. Ta situacija je češća tijekom montaže cijevi, posebno na mjestima poput zakrivljenja i spojeva cijevi, gdje je cinski sloj oštećen zbog čestog radnje.
Problemi s kvalitetom galvanizacije:
Efekt proti koroziji oksidiranih cijevi je izravno povezan s debljinom i jednolikostjo galvanizacijske sloja zinca. Ako je proces proizvodnje oksidirane cijevi nekvalificiran, što uzrokuje nejednoliku debljinu sloja zinca ili lošu lepljenost sloja zinca, može doći do toga da se na nekim dijelovima otvori površina čelika, povećavajući rizik od korozije.
- Neravna debljina sloja zinca: Ako je debljina sloja zinca neravnomjerana tijekom galvanizacijskog procesa, slabi dijelovi su podložni koroziji.
- Loša lepljenost sloja zinca: Galvanizirani sloj nije čvrsto spojen s površinom čelične cijevi, a lako se može odlupiti pod djelovanjem vanjskih sila, uzrokujući da cijev postane rđava.
- Defektni galvanizacijski proces: Tijekom procesa toplice galvanizacije, ako je temperatura zinčane bašte nestabilna, vrijeme toplice predugačko ili prekratko, kvaliteta sloja zinca će smanjiti, a mogu se čak pojaviti defekti na površini cijevi.
Utjecaj okolišnih faktora:
Rzava galvaniziranih cijevi je također u bliskom vezi s okruženjem u kojem se nalaze.
- Vlažnost i klima: Visoka vlažnost i vlaga u klimalnim uvjetima ubrzavaju proces oksidacije zinčane plasti, posebno pri čestim promjenama temperature, na površini cijevi nastaje kondenzat i obrazuju se kapljice vode, što dalje ubrzava koroziju.
- Korozija soljanim štitom: Cijevi kod mora ili u soljano-alkalne područje su posebno osjetljive na koroziju uzrokuju soljanim štitom. Soljani štit se priljepi na površinu cijevi, stvarajući elektrolitsko okruženje, što dovodi do lakoće korozije zinčane plasti, što izlaganje baze metala i zatim rzavi.
- Kisela i bazna okruženja: Okruženja koji sadrže kiseline i bazne plinove kao što su industrijske zone i kemikalne tvornice također će ubrzati koroziju galvaniziranih cijevi. Korozivne tvari poput kiselnih plinova, sulfida i chlorida imaju jak utjecaj na galvanizirane cijevi.
Utjecaj kvalitete vode:
Kvaliteta vode je izravno povezana s brzinom korozije galvaniziranih cijevi. U nekim vrlo korozivnim vodnim okruženjima (poput vodenih izvora koji sadrže više kiselog materijala), čak i galvanizirane cijevi teško mogu izbjegnuti rđavinu.
- PH vode: pH vode izravno utječe na brzinu korozije galvaniziranih cijevi. Kisela voda (pH vrijednost ispod 7) ima jak korozivan učinak na zinčan sloj, uzrokujući da se zinčan sloj rastvara.
-
Tvrda i meka voda: Tvrda voda sadrži više minerala (poput iona kalcija i magnezija). Dugo vrijeme prijevoza kroz galvanizirane cijevi može lako formirati oštruge na unutrašnjoj strani cijevi, što podstiče koroziju. Meka voda obično je aktivnija i lako reagira s zincom, ubrzavajući rastvaranje zinca.
- Korozivne tvari: Kada voda sadrži korozivne tvari kao što su sulfid i amonijak, brzina korozije galvaniziranih cijevi će se ubrzati, a čak i uzrokovati ozbiljnu prometnu propust.
Elektrokemikaljska korozija:
Fenomen elektrokemijskog koroziranja uzrokuje se razlikom potencijala koja nastaje kada se različiti metali dodirnu u elektrolitskom okruženju, što rezultira korozijom metala. U sustavu cijevi s galvanizacijom, elektrokemijska korozija glavnoprije sve odgovara u sljedećim situacijama:
- Dodir različitih metal: Kada je galv pipe u direktnom kontaktu s drugim metalima (poput bakra, aluminija itd.), zbog postojanja razlike u potencijalu, cinko kao žrtvanski anoda će se korozirati prije drugih metala, što rezultira ubrzanim korozijom galvanizirane cijevi.
- Spajanja cijevi: Na spajanjima cijevi, zaštite kabla i drugim mjestima, često se nagomilava struja ili razlika potencijala, što ubrzava reakciju korozije.
Slabnjenje efekta žrtvanskog anoda cinkove slojeve:
Iako može učinkovito sprečiti koroziju žrtveni anodni efekat cinka, kada je sloj cinka pretežak ili prematurno potrošen u korozivnom okruženju, žrtveni anodni efekat će oslabiti, što rezultira otkrivanjem matrice čevanja od čelika, time povećavajući rizik od puca.
- Nedovoljna debljina sloja cinka: Ako je sloj cinka na galvaniziranom cijevi preuzak, zaštitni efekat cinka brzo propadne i proces korozije čelika će se ubrzati.
- Prematura potrošnja sloja cinka: Tijekom dugoročnog korištenja, posebno u vrlo korozivnom okruženju, sloj cinka se troši prebrzo, žrtveni anodni efekat se oslabljava, a matrica čevanja od čelika se postepeno otkriva.
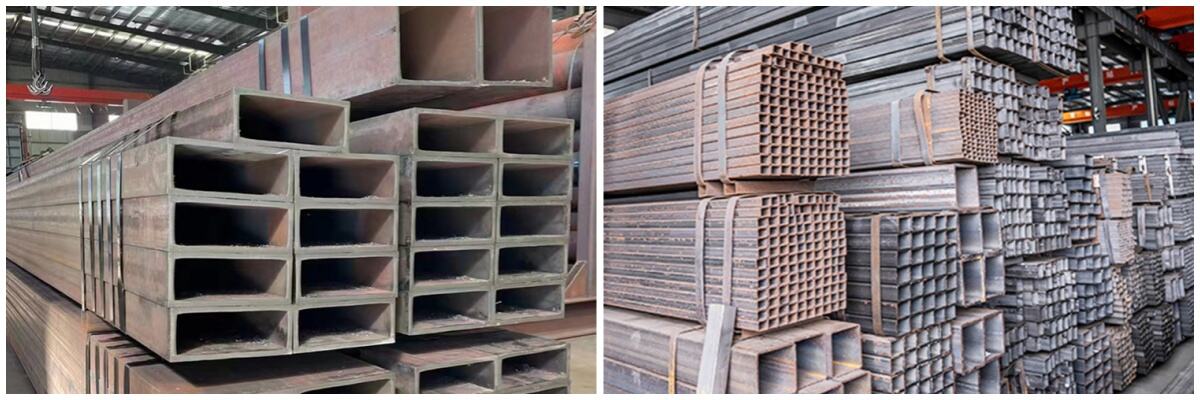
Utjecaji puca na galvanizirana cijevi
1). Smanjena trajnost cijevi: Jednom galv cijevi kada su oksidirani, njihova nosivost, otpornost na tlak i udarna čvrstoća će se smanjiti, a njihov radni život bit će znatno skraćen. Starenje cijevi uzrokovano korozijom čini da cijevi nisu u stanju izdržati naporne opterećenja pod visokim tlakom vode ili drugim radnim uvjetima, a lako mogu praskati ili propustiti.
2).Zagađivanje vode: Zincna zagađenja uzrokovana korozijom galvaniziranih cijevi mogu imati negativan utjecaj na okoliš. Posebno u javnim vodovodnim sustavima, promak zincnog iona može uzrokovati zagađenje vode i utjecati na sigurnost pitke. Pored toga, promak iz ržavih cijevi može zagađivati okolnu tlo i biljnu svijetlost, što utječe na ekološko okruženje.
3).Pretnje strukturnoj sigurnosti: Rozbijanje galvaniziranih cijevi ne utječe samo na same cijevi, već također mogu utjecati na nosnu strukturu cijevi. Na primjer, u područjima elektriciteta i komunikacija, galvanizirane cijevi se često koriste za podršku i zaštitu kabela. Ako su galvanizirane cijevi ozbiljno rozbijene, može dovesti do preloma kabela ili štete vanjskom zaštitnom sloju, što zauzvrat utječe na stabilnost i sigurnost cijelog sustava.
Mjere protiv rozbijanja galvaniziranih cijevi
Poboljšanje kvalitete galvanizacije
Osiguravanje da je jednolikost, debljina i lepljenje cinka u skladu s standardima može znatno poboljšati otpornost galvaniziranih cijevi na rozbijanje. Tijekom proizvodnje treba strogo kontrolirati temperaturu, koncentraciju i druge postupne parametre galvanizacijskog rastvora kako bi se osigurala kvaliteta sloja cinka.
Spriječiti mehaničku štetu
Stalno štetno utjecanje i iznosenost trebaju se sprečiti tijekom prijevoza, montaže i uporabe cijevi. Kada je površina cijevi s galvanizacijom udarena, oštećena ili sudarila se, zinčana sloj lako može biti oštećen, što otvara bazni metal čeljustne cijevi, što uzrokuje koroziju. Zbog toga, bude oprezan tijekom procesa montaže kako bi se izbjeglo oštećenje zinčanog sloja. Stalno štetno utjecanje može se smanjiti sljedećim mjerama:
- Koristite meke materijale za pakiranje: Tijekom prijevoza i manipulacije, koristite meke zaštitne materijale poput pjenova, plastinih filmova itd. da biste omotali cijevi kako biste smanjili sudar i trenje.
- Izbjegavajte direktno udaranje tijekom montaže: Koristite profesionalne alate za montažu poput držača i cijevi da biste izbjegli direktno udaranje na cijevi.
Antikorozioni oblog i dodatna galvanizacija
Za mjesta gdje je galvanizirana metalna cijev ako se koristi u oštrom okruženju, na vanjsku stranu cijevi se mogu primijeniti dodatni protizakrnjivi oblozi. Ti oblozi su obično napravljeni od materijala poput epoksidne tinte, poliuretana, polietilena itd., što može još više poboljšati protizakrnjivu performansu i produžiti životnu dobu galvanizirane cijevi.
- Epoksidni oblog: Ima dobru lepljivost i otpornost na zakrnju i prilagođen je zahtijevanim industrijskim okruženjima.
- Polietileni oblog: Za zakopane cijevi, polietileni oblog efektivno sprečava pronikavanje vlažnosti, kiseline i baze te sprečava zakrnju.
Pored toga, u nekim posebnim slučajevima, kada je cinkov sloj djelomično oštećen, može se koristiti metoda ponovnog galvaniziranja kako bi se popravila oštećena područja i vraćena protizakrnjiva sposobnost cijevi.
Jačanje kontrola okoline
Prilikom odabira cijevi s galvanizacijom potrebno je uzeti u obzir njihovu okolinu montaže. Za cijevi koje su izložene vlažnim uvjetima, visokoj solenoj raspršnji, kiselinama ili baznim okolinama, treba odabrati cijevi s većom otpornosti na koroziju, ako je to moguće, ili preuzeti neke mjere za kontrolu okoline.
- Smanjite izlaganje područjima visoke vlage: Na primjer, u vlažnim područjima ili otvorenom prostoru, pokušajte uzeti mjere kako biste smanjili vrijeme i površinu izlaganja cijevi, poput izgradnje sklonista, stropova itd.
- Unaprijedite uvjete ventilacije: Stjecanjem jačeg zračnog cirkulacije, smanjuje se zadržavanje vlage na površini cijevi te se usporava korozivna reakcija.
Redovne provjere i održavanje
Putem redovnih inspekcija, problemi s korozijom mogu se pronaći u vrijeme i preuzeti popravni radovi. Sadržaj inspekcije uključuje cjelovitost galvaniziranog sloja, da li je površina odlupljena ili prska, te da li postoji nagomiljena voda ili škrljavina unutar cijevi.
- Redovna inspekcija: Za otkrivena galvanizirana cijevi, inspekcijske radnje se mogu izvoditi svakih šest mjeseci ili godišnje, posebno na spojevima cijevi, vratima, flancama i drugim dijelovima kako bi se provjerilo postojanje korozije ili štete.
- Unutarnja inspekcija: Za galvanizirane cijevi koje su zakopane ili ne mogu se direktno promatrati, stanje unutarnje zida cijevi može se utvrditi pomoću endoskopske inspekcijske tehnike, ultrazvučnog testiranja i drugih metoda.
Korištenje inhibitora korozije
U nekim cjevnim sustavima, posebno u vodovodnim cijevima ili cijevima za plin, mogu se koristiti inhibitori korozije kako bi se smanjio događaj korozije. Ti inhibitori obično sprečavaju napredak reakcija korozije mijenjanjem kemijskog okruženja unutar i izvan cijevi.
- Obrada kvalitete vode: Za galvanizirane cijevi u vodovodnim cijevima, mogu se koristiti metode poput mekaniziranja vode, uklanjanja disperziranog kisika i korozivnih iona iz vode i druge metode kako bi se smanjila vjerojatnost korozije.
- Zaštitno plinovo: U cijevima za prijenos plina, u nekim slučajevima može biti unesen određeni zaštitni plin kako bi se promijenila sastavnica ili tlak plina te usporen korozivni proces.
Izaberite odgovarajuće materijale za cijevi
Za cjevne sustave koji su izloženi ekstremnim uvjetima dugo vrijeme, pored galvaniziranih cijevi, postoje i drugi materijali s jačom otpornostiu na koroziju. Na primjer, PVC cijevi, PE cijevi, nerustingajuće cijevi itd., ti materijali imaju bolju otpornost na koroziju od galvaniziranih cijevi i posebno su prilagođeni nekim posebnim primjenama.
- Nerustingajuće cijevi: Nerustingajući čelik ima jaku otpornost na koroziju i dug trajanje, a pogodan je za situacije gdje je potrebna vrlo visoka otpornost na koroziju.
- PE cijevi, PVC cijevi: Ti plastični materijali za cijevi imaju dobru otpornost na koroziju i posebno su prilagođeni prijenosu tekućinskih sredstava poput vode i plina.
Oxid galvaniziranih cijevi je uobičajeni problem, ali putem razumnog izbora materijala, izgradnje i održavanja, se korisni život galvaniziranih cijevi može učinkovito produžiti.
Mi smo profesionalni proizvođač čelika. Ako imate bilo kakve potrebe, možete nas kontaktirati bilo kada!
+86 17611015797 (WhatsApp )
info@steelgroups.com