لوله گالوانیزه یک ماده رایج برای ساخت و صنعت است. سطح آن با لایهای از روی پوشانده شده است تا عناصر آهنی درون لوله فولادی از تماس با هوا و رطوبت بیرونی جلوگیری شود، که نقش ضد خوردگی و ضد خوردگی را ایفا میکند. با این حال، بسیاری از کاربران مشاهده کردهاند که لولههای فولادی زنگاله شده ممکن است هنوز خورد میخورند در حین استفاده از لولههای زنگاله شده. پس، چرا لوله زنگاله شده خورد میخورد؟ علت خوردگی لولههای زنگاله شده چیست؟ و خوردگی آن چه تأثیری بر استفاده واقعی دارد؟ این مقاله این مسائل را به طور دقیق توضیح خواهد داد و امیدوارم که برای شما مفید باشد.
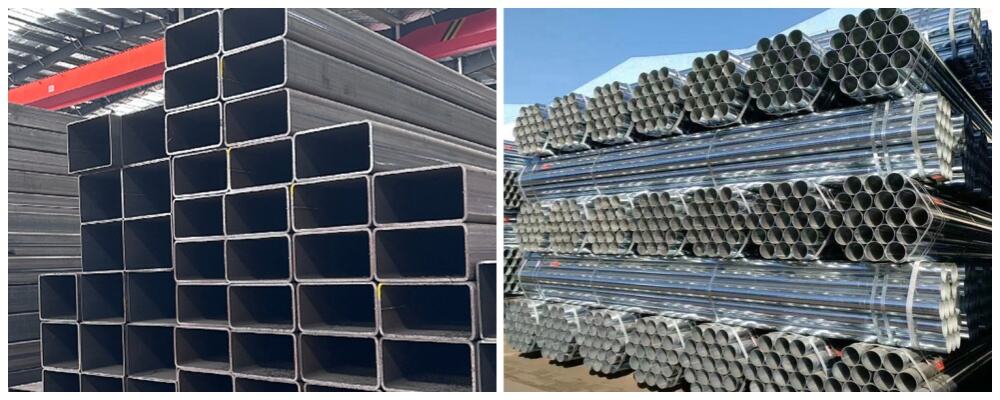
چیست لوله زنگاله شده؟
لوله روغنی، نوعی لوله است که با پوشاندن لایهای از روی بر روی سطح لوله فولادی، لایهای ضد خوردگی ایجاد میکند تا مقاومت ضد خوردگی لوله را افزایش دهد. هدف از روغنی کردن جلوگیری از خوردگی اکسیداتیونی لوله خود به دلیل تماس با محیطهایی مانند هوا و آب است. به ویژه در محیطهای سخت استفاده مانند رطوبت و شوری، لایه روغنی حفاظت قویای فراهم میآورد.
بر اساس فرآیندهای مختلف روغنی کردن، لولههای روغنی به دو دسته لولههای روغنی گرم و لولههای روغنی الکتریکی تقسیم میشوند.
- لوله روغنی گرم: فرآیند روغنی گرم شامل گرم کردن لوله فولادی تا دماهای مشخص و غوطه ور کردن آن در ظرفی حاوی روی مایع است. از طریق واکنشهای شیمیایی، لایه روی با سطح لوله فولادی ترکیب میشود و لایه آلیاژ زغال روی-آهن را تشکیل میدهد. ضخامت لایه روی در لولههای روغنی گرم بیشتر است، معمولاً تا 60 تا 80 میکرون، و مقاومت عالی ضد خوردگی دارد.
- لوله الکتروگالوانیز: لایه روغن روی سطح لوله فولادی توسط روش الکترودوزی یا پاشیدن قرار میگیرد. ضخامت لایه روغن در لوله الکتروگالوانیز نسبتاً کم است و معمولاً بین 5 تا 15 میکرون قرار دارد. هرچند که اثر ضد زنگ خوردن آن به اندازه گالوانیزه گرم خوب نیست، اما یکنواختی لایه روغن در طی فرآیند قابل کنترل است.
اصل ضد زنگ خوردن گالوانیز
اصل ضد زنگ خوردن لوله گالوانیز بر اساس اثر "آنود قربانی" روغن است. فعالیت فلزی لایه روغن قوی است. وقتی سطح لوله با محیط خارجی مواجه میشود، روغن ابتدا واکنش اکسیداسیون را شروع میکند و رویزن (ZnO) تشکیل میدهد. این لایه رویزن میتواند نفوذ اکسیژن و رطوبت را جلوگیری کند و بدنه لوله فولادی را از زنگ خوردن محافظت کند.
چرا لوله گالوانیز ثانیه زنگ میخورد؟
هرچند لایه زینک لولههای آبرسانی در نظریه میتواند به طور مؤثر ضد فساد باشد، اما در عمل، صدف زنی همچنان ممکن است رخ دهد. دلایل صدف زنی لولههای آبرسانی معمولاً به شرح زیر است:
آسیب به لایه زینک:
لایه محافظ سطح لولههای آبرسانی از لایه زینک تشکیل شده است. اگر لایه زینک تحت تأثیر برخورد مکانیکی، سوزنی، جراحی و عوامل دیگر قرار گیرد، لایه زینک ممکن است از بین برود یا شکسته شود و سطح لوله فولادی که نشان داده شده است به محیط خارجی معرض حمله قرار میگیرد و ممکن است فاسد شود. این وضعیت در طی نصب لولهها شایعتر است، به ویژه در مکانهایی مانند زاویههای لوله و جوینتها، که لایه زینک به دلیل عملیات مکرر آسیب میبیند.
مشکلات کیفیت زینککاری:
اثر ضد خوردگی لولههای زنکبیده به صورت مستقیم با ضخامت و یکنواختی لایه زنگ آن مرتبط است. اگر فرآیند تولید لوله زنکبیده نامعتبر باشد که منجر به ناهمواری در ضخامت لایه زنگ یا ضعف در چسبندگی لایه زنگ شود، ممکن است برخی نقاط سطح لوله فولادی را نشان دهد و خطر خوردگی را افزایش دهد.
- ناهمواری در ضخامت لایه زنگ: اگر ضخامت لایه زنگ در طی فرآیند زنکبی نامنظم باشد، مناطق ضعیف عرضه خوردگی میشوند.
- چسبندگی ضعیف لایه زنگ: لایه زنکبیده به درستی به سطح لوله فولادی چسبیده نشده و تحت تأثیر نیروی خارجی به راحتی از بین میرود که باعث خوردگی لوله میشود.
- عیوب در فرآیند زنکبی: در طی فرآیند زنکبی گرم، اگر دماي ظرف زنگ ثابت نباشد، زمان غوطه ور کردن طولانی یا کوتاه باشد، کیفیت لایه زنگ کاهش مییابد و حتی عیوب روی سطح لوله تشکیل میشود.
تأثیر عوامل محیطی:
زیر خورد گالوانیزه شده نیز به طور نزدیکی با محیطی که در آن قرار دارند مرتبط است.
- رطوبت و اقلیم: رطوبت بالا و شرایط اقلیمی مرطوب فرآیند اکسیداسیون لایه روی را شتاب میدهد، به ویژه تحت تغییرات مکرر دما، سطح لوله به راحتی عرضه تراشیدگی میشود و قطرههای آب تشکیل میدهد، که بیشتر به زیر خورد منجر میشود.
- زیر خورد پاشنده شور: لولههای نزدیک دریا یا مناطق شور-کلری به طور خاص عرضه زیر خورد پاشنده شور هستند. پاشنده شور به سطح لوله چسبیده و محیط الکترولیتیجاد میکند، که باعث میشود لایه روی به راحتی زیر خورد شود، باعث نمایش فلز پایه و سپس زیر خورد شدن آن میشود.
- محیط حامض و قلیایی: محیطهای حاوی گازهای حامض و قلیایی مانند مناطق صنعتی و کارخانجات شیمیایی نیز به زیر خورد لولههای گالوانیزه شده شتاب میدهند. مواد زیر خورده کننده مانند گازهای حامض، سولفیدها و کلریدها تأثیر زیر خورد کننده قوی بر لولههای گالوانیزه دارند.
تأثیر کیفیت آب:
کیفیت آب به صورت مستقیم با نرخ فرسایش لولههای زنگینی مرتبط است. در برخی محیطهای آب فرسایشزا (مانند منابع آب حاوی مواد اسیدی بیشتر)، حتی لولههای زنگینی نیز سخت میتوانند ریزش را جلوگیری کنند.
- PH آب: pH آب به طور مستقیم بر روی نرخ فرسایش لولههای زنگینی تأثیر میگذارد. آب اسیدی (مقدار pH کمتر از 7) تأثیر فرسایشزا قویای بر لایه زغال سنگ دارد و باعث حل شدن لایه زغال سنگ میشود.
-
آب سخت و آب نرم: آب سخت شامل میزان بیشتری از معادن (مانند یونهای کلسیوم و مغنز) است. حمل طولانیمدت آب سخت از طریق لولههای زنگینی میتواند باعث تشکیل خاکستر روی دیواره داخلی لوله شود، که این موضوع فرسایش را تقویت میکند. آب نرم معمولاً فعالتر است و به راحتی با زغال سنگ واکنش نشان میدهد و حل زغال سنگ را شتاب میدهد.
- مواد فرسایشزا: هنگامی که آب مواد فرسایشزا مانند سولفید و آمونیاک را در بر دارد، نرخ فرسایش لولههای زنگینی افزایش مییابد و حتی میتواند به علت فرسایش شدید،-Leakage خطیرواقع شود.
فرسایش الکتروشیمیایی:
پدیده فرسایش الکتروشیمیایی به دلیل تفاوت پتانسیل حاصل از تماس فلزات مختلف در محیط الکترولیتی رخ میدهد، که باعث فرسایش فلز میشود. در سیستم لولههای زنگالهدار، فرسایش الکتروشیمیایی عمدتاً در شرایط زیر رخ میدهد:
- تماس فلزات مختلف: هنگامی که لوله زنگالهای در تماس مستقیم با فلزات دیگر (مانند مس، آلومینیوم و غیره) قرار گیرد، به دلیل وجود تفاوت پتانسیل، روی به عنوان آنود قربانی قبل از فلزات دیگر فرسوده میشود، که باعث شتاب بخشیدن به فرسایش لوله زنگالهدار میشود.
- جoints لوله: در جوینتهای لوله، لولههای محافظ کابل و مکانهای دیگر، جریان یا تفاوت پتانسیل اغلب تجمع مییابد، که واکنش فرسایشی را شدت میبخشد.
ضعف اثر آنود قربانی لایه روی:
اگرچه اثر آنود قربانی زینک میتواند به طور مؤثری تاوان جلوگیری از خوردگی را داشته باشد، اما هنگامی که لایه زینک بسیار نازک است یا در محیط خوردگیزا به طور مقدماتی مصرف شود، اثر آنود قربانی ضعیف میشود و این باعث میشود که ماتریس لوله فولادی آشکار شود و در نتیجه خطر خوردگی افزایش یابد.
- ضخامت ناکافی لایه زینک: اگر لایه زینک لوله گالوانیزه بسیار نازک باشد، اثر محافظ زینک به سرعت ناکارآمد میشود و فرآیند خوردگی لوله فولادی شتاب میگیرد.
- مصرف مقدماتی لایه زینک: در استفاده بلندمدت، به ویژه در محیطهای خوردگیزا، لایه زینک به سرعت مصرف میشود، اثر آنود قربانی ضعیف میشود و ماتریس لوله فولادی به تدریج آشکار میشود.
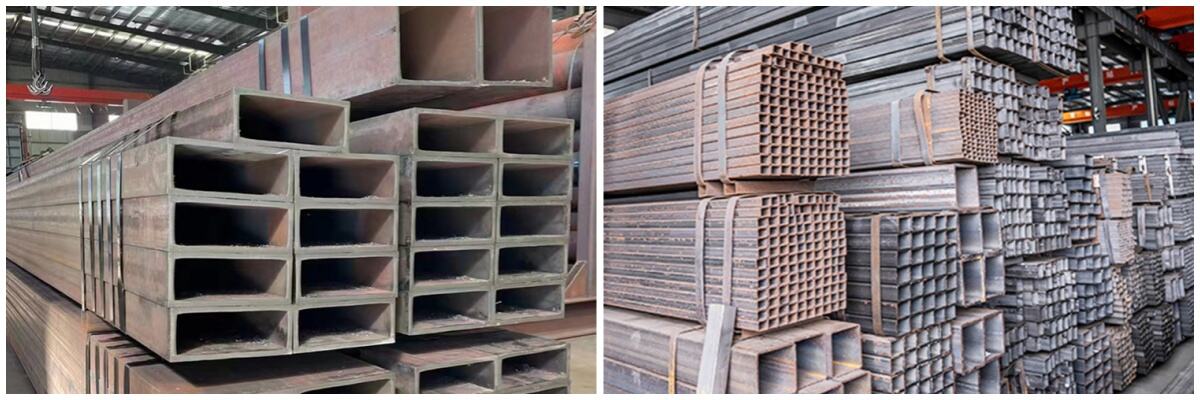
اثرات خوردگی بر روی لولههای گالوانیزه
۱) کاهش استحکام لولهها: یکبار galv pipes اگر لولهها خوردگی داشته باشند، ظرفیت باربری، مقاومت فشار و مقاومت در برابر ضربه آنها کاهش مییابد و طول عمر آنها به شدت کاهش مییابد. قدیمی شدن لوله ناشی از خوردگی آن را ناتوان میسازد تا تنش را تحت جریان آب فشار بالا یا شرایط کاری دیگر تحمل کند و به راحتی ممکن است شکسته یا حفر شود.
2). آلودگی آب: آلودگی زینک ناشی از خوردگی لولههای زینکپوش ممکن است تأثیر منفی بر محیط زیست داشته باشد. به ویژه در سیستمهای تأمین آب شهری، رشح زینک ممکن است منجر به آلودگی آب و تأثیر بر امنیت آب قابل مصرف شود. علاوه بر این، رشح ناشی از لولههای خوردگی ممکن است آلودگی خاصی به خاک و گیاهان اطراف ایجاد کند و محیط زیست را تحت تأثیر قرار دهد.
3). تهدید به امنیت سازهای: زیرخورد لولههای زنگاله شده تنها لولهها را تحت تأثیر قرار نمیدهد، بلکه ممکن است سازه حامل لولهها را نیز به خطر بیندازد. به عنوان مثال، در حوزههای برق و ارتباطات، لولههای زنگاله شده اغلب برای پشتیبانی و محافظت از کابلها استفاده میشوند. اگر لولههای زنگاله شده به شدت زیرخورد شوند، ممکن است منجر به شکستن کابلها یا آسیب به لایه محافظتی خارجی شود که به نوبه خود ایمنی و پایداری کل سیستم را تحت تأثیر قرار میدهد.
اندازهگیریهای ضد زیرخورد برای لولههای زنگاله شده
بهبود کیفیت فرآیند زنگاله کردن
تضمین یکنواختی، ضخامت و چسبندگی لایه روی به معیارها میتواند توانایی مقاومت علیه زیرخورد لولههای زنگاله شده را به طور قابل توجهی افزایش دهد. در طی فرآیند تولید، دما، غلظت و سایر پارامترهای فرآیند محلول زنگاله باید به صورت دقیق کنترل شوند تا کیفیت لایه روی تضمین شود.
پیشگیری از آسیب مکانیکی
آسیب مکانیکی و سایش باید در حین حمل، نصب و استفاده از لوله جلوگیری شود. هنگامی که سطح لوله زنگاله شده تحت تأثیر ضربه، خراش یا برخورد قرار گیرد، لایه روی به راحتی آسیب میپذیرد و فلز پایه لوله فولادی عرضه میشود، که این موضوع باعث صدفزدگی آسان میشود. بنابراین، در طی فرآیند نصب دقت کنید تا آسیب به لایه روی را جلوگیری کنید. آسیب مکانیکی میتواند با اقدامات زیر کاهش یابد:
- استفاده از مواد بستهبندی نرم: در حین حمل و نقل و دستهبرداری، از مواد محافظ نرم مانندフォーム، فیلم پلاستیکی و غیره برای بستهبندی لوله استفاده کنید تا از برخورد و سایش جلوگیری شود.
- جلوگیری از ضربه مستقیم در حین نصب: از ابزارهای نصب حرفهای مانند دوکان لوله و کلیپها استفاده کنید تا از ضربه مستقیم به لوله جلوگیری شود.
پوشش ضد صدفزدگی و لایه زنگاله تکمیلی
برای مکانهایی که لوله فلزی زنگاله شده اگر در محیط سختی استفاده شود، میتوان پوششهای اضافی ضد زنگخوردن به بیرون لوله اعمال کرد. این پوششها معمولاً از موادی مثل رزین اپوکسی، یورتان، پلیاتیلن و غیره ساخته میشوند که میتوانند عملکرد ضد زنگخوردن را افزایش داده و طول عمر لوله زنگدار را افزایش دهند.
- پوشش اپوکسی: دارای چسبندگی خوب و مقاومت علیه فرسایش است و برای محیطهای صنعتی سخت مناسب است.
- پوشش پلیاتیلن: برای لولههای مدفون، پوشش پلیاتیلن میتواند به طور مؤثر ورود آب و مادههای اسیدی و قلیایی را جلوگیری کرده و زنگخوردن را پیشگیری کند.
علاوه بر این، در برخی موارد خاص، هنگامی که لایه زغالهای به طور جزئی آسیب دیده باشد، میتوان از روش زغالهزنی مجدد برای تعمیر ناحیه آسیبدیده و بازگرداندن توانایی ضد زنگخوردن لوله استفاده کرد.
تقویت کنترل محیطی
هنگام انتخاب لولههای زنگاله شده، لازم است به محیط نصب آنها توجه کنید. برای لولههایی که به محیطهای مرطوب، مغشوش با بخاخ سنگین، یا حاوی اسید یا قلیایی معرض قرار دارند، باید هرچند ممکن لولههایی با مقاومت بالاتر ضد خوردگی انتخاب شوند یا تدابیری برای کنترل محیط انجام شود.
- کاهش مواجهه با مناطق رطوبت زیاد: به عنوان مثال، در مناطق مرطوب یا محیطهای آزاد، سعی کنید تدابیری اتخاذ کنید تا زمان و مساحت معرض قرار گرفتن لوله را کاهش دهید، مانند ساخت پناهگاهها یا سقفها.
- بهبود شرایط تهویه: با تقویت جریان هوا، رطوبت مانده روی سطح لوله کاهش یافته و واکنش خوردگی کندتر میشود.
بررسی و نگهداری منظم
با انجام بررسیهای منظم، مشکلات خوردگی میتوانند به موقع شناسایی شده و تدابیر تعمیری انجام شود. محتوای بررسی شامل کامل بودن لایه زینک، اینکه آیا سطح لوله پیچیده یا شکسته شده است، و آیا آب جمع شده یا رسوب در داخل لوله وجود دارد یا خیر، میشود.
- بررسی منظم: برای لولههای زنگین شده که به صورت آشکار نصب شدهاند، میتوان هر شش ماه یا سالی یک بار بررسی انجام داد، به ویژه در محل اتصالات لوله، خمها، فلنسها و قسمتهای دیگر برای بررسی فساد یا آسیب.
- بررسی داخلی: برای لولههای زنگین شده که مدفون هستند یا نمیتوان به طور مستقیم مشاهده کرد، وضعیت دیواره داخلی لوله میتواند از طریق روشهایی مانند بررسی با اندازهگیری دوربینی، تست اولتراسونیک و غیره فهمیده شود.
استفاده از مهارکنندههای فساد
در برخی از سیستمهای لولهای، به ویژه لولههای آب یا گاز، میتوان از مهارکنندههای فساد استفاده کرد تا از رخداد فساد جلوگیری شود. این مهارکنندهها معمولاً با تغییر محیط شیمیایی داخل و خارج از لوله، پیشرفت واکنشهای فساد را متوقف میکنند.
- مدیریت کیفیت آب: برای لولههای زنگین شده در لولههای آب، میتوان از روشهایی مانند نرمکردن آب، حذف اکسیژن محلول و یونهای فسادآفرین در آب استفاده کرد تا احتمال فساد را کاهش دهد.
- محافظت گازی: در لولههای انتقال گاز، میتوان گازهای محافظتی تزریق کرد تا ترکیب یا فشار گاز را تغییر داده و خوردگی را کاهش دهد.
انتخاب مواد مناسب برای لولهها
برای سیستمهای لولهای که به محیطهای شدید در طول مدت معرض قرار میگیرند، علاوه بر لولههای زنگدار، مواد لولهای دیگری نیز موجود هستند که مقاومت بیشتری نسبت به خوردگی دارند. به عنوان مثال، لولههای PVC، لولههای PE و لولههای فولاد راستگرما، این مواد مقاومت بهتری نسبت به خوردگی نسبت به لولههای زنگدار دارند و به ویژه برای کاربردهای ویژه مناسب هستند.
- لولههای فولاد راستگرما: فولاد راستگرما مقاومت قوی خوردگی دارد و عمر کاربردی بلندی دارد و مناسب جایگاههایی است که نیازمند مقاومت بسیار بالای خوردگی هستند.
- لولههای PE، لولههای PVC: این مواد لوله پلاستیکی مقاومت خوبی نسبت به خوردگی دارند و به ویژه برای حمل میانههای مایع مانند آب و گاز مناسب هستند.
زنگ زدن لولههای پوششدهی شده با روی یک مشکل رایج است، اما با انتخاب منطقی مواد، ساخت و نگهداری، میتوان عمر کاربردی لولههای پوششدهی شده با روی را به طور مؤثر افزایش داد.
ما تولیدکننده حرفهای فولاد هستیم. اگر نیازی دارید، میتوانید هر زمان ما را تماس بگیرید!
+86 17611015797 (WhatsApp )
info@steelgroups.com